He Built One of the First Barndos Out There
By Linda Schmid
Speaking to some admirers of barndominiums about these efficient, open-spaced homes, you might think they just came on the market last year. Not so. David Gruhlke has been living in a barndominium since the 1980s.
Barndo #1
Gruhlke relates that while driving one day, he stopped to admire a new pole barn building, the symmetry, complementary colors, overhangs, the perfection of the details. Gruhlke thought: “that is one good looking pole barn,” and then he thought, “I could live in that.”
He contemplated this. Was it a realistic plan? At the time he had never heard of anyone living in a post-frame house, but he knew enough about construction and pole barns (his family and neighbors had them built) to have no qualms about safety or his ability to make this idea happen. He also knew that building a house this way would save him money. So he thought about what he really wanted. He decided on a piece of land where he could snowmobile, and a house with a big, finished shop.
However, the inspection people at County Zoning had never heard of such a thing either. They said they couldn’t approve a post-frame building for people to live in. But they saw the plans, it met the codes, and since they couldn’t find anything wrong with it, they finally had to approve it.
So Gruhlke, got started on his project. First he found a nice 13-acre parcel of land, and he cleared a spot among the trees for his new home. He was working full time, so he did the General Contracting and sub-contracted out the majority of the work, including the framing and sheathing. The house was about 800 square feet, on a slab with an attached shop, about 1000 square feet. It’s a simple ranch with a sloped roof and metal siding with a cedar front for accent. Gruhlke didn’t have the budget for bells and whistles, so he kept it simple by necessity.
Of course, one of the advancements that has made post-frame barndominiums more common today is protection for wooden posts.
“There were no special protections for posts at the time,” Gruhlke said. “I used 6×6 treated wooden posts.”
However, Gruhlke had no major challenges with the building of his barndo, nor did he have issues living in it. In fact, it worked out well, was energy efficient, and people who saw his home liked it. Gruhlke grabbed hold of the opportunity he saw and began selling barndominiums under the name Homework Design. However, it was slow going. Part of the reason was because it was a new idea, and people are often slow to adapt to new ideas, especially when it comes to their homes. But the other part of the problem was a lingering question about the design of these homes; the wood posts were in contact with the ground, which sooner or later leads to problems.
So Gruhlke got to work and developed Plasti-Sleeve. This is a plastic sleeve molded to fit a particular size post. The builder slides it on before putting the treated post in the ground, thereby creating a barrier from ground elements, extending post life. This made selling his post-frame homes a little easier.
Gruhlke was happy with his barndo until he began a family. At 800 square feet, it was a little close so he and his wife considered getting a bigger house, but before they did anything about it something completely unexpected happened. Gruhlke got into an accident. He survived and he was left partially paralyzed.
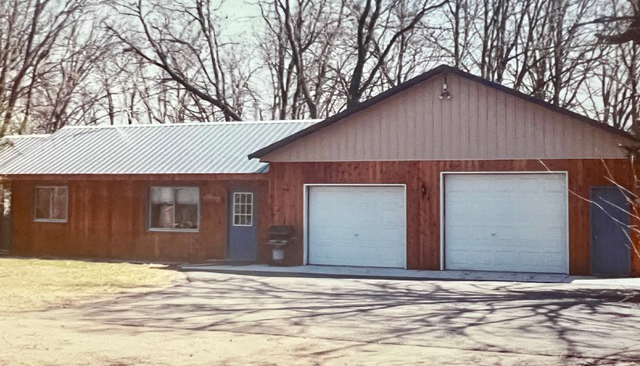
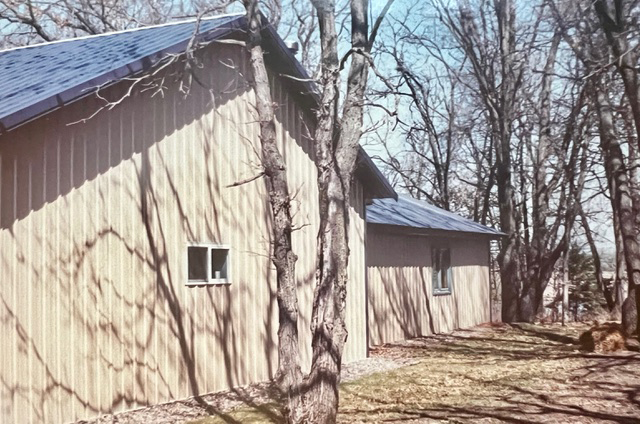
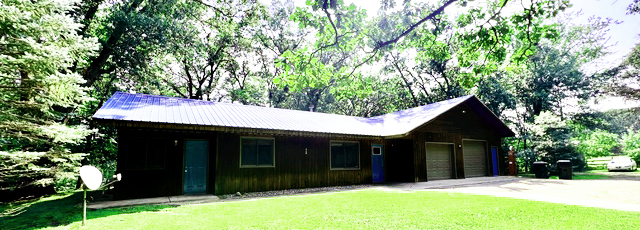
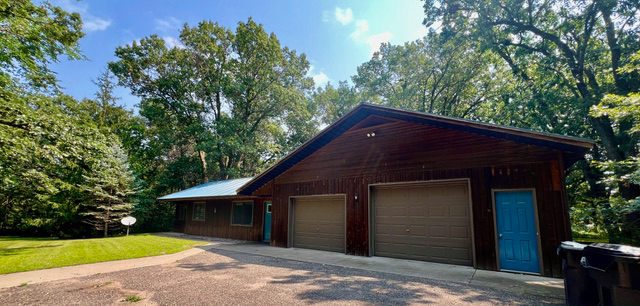
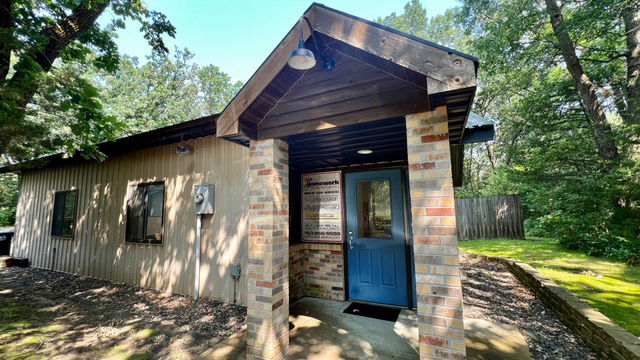
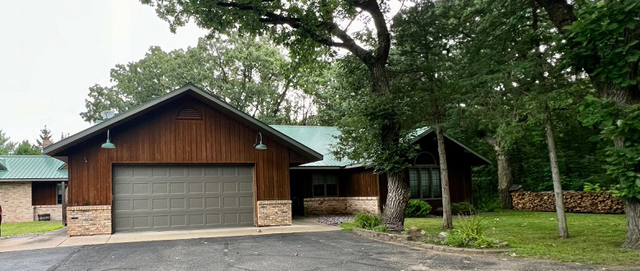
Barndo #2
They now had reason to move forward quickly as their bathroom was not accessible for Gruhlke’s wheelchair. They decided to build a bigger home on the same property they were living on, making it accessible with a custom shower, wider hallways and doorways, and grab bars in the bathroom.
The second barndominium was begun with Homework Design as the General Contractor. They built a 2,400 square foot ranch home and some nice upgrades from his first barndo. The concrete slab featured in-floor heat which is a welcome thing on a snowy winter day, plus a partial basement which is nice for sheltering from a storm. The design included a family room and a game room, and a spa-style room with a hot tub.
Efficiency and durability were enhanced with protected posts, insulation was upgraded from cellulose which can settle to blown-in fiberglass in the ceiling. Further the entire shell is sheathed under the siding, and the roof was sheathed with plywood and underlayment with 26 gauge metal roofing.
The house features lots of wood, including a knotty pine vaulted ceiling in the reat room, antique wood stoves, bricked walls, and ceramic or laminate for wheeling ease,plus vaulted ceilings with tongue and groove in the master bedroom. The spa room has a sunken floor for accessibility, accented by cedar decking.
The build went well; it was done in 5 months. This left the old barndo empty, so he rented part of it out and remodeled the shop portion to create a great office space for his company in the front.
Barndo #3?
The family enjoyed barndominium living. Now the kids have grown and moved on, though, and the house feels a bit big. Gruhlke is thinking about building…a barndominium, of course. This house would be somewhere between the sizes of his first two barndos, somewhere around 1500 square feet of living space he is thinking. He would also like an 8-10 car attached garage to have his car collection, recreation vehicles, and shop all under one roof.
Advice From One Barndo Enthusiast to Another
Gruhlke said that many folks think it’s going to be much cheaper to build a barndominium than other types of builds. He said that if you accent the exterior with brick or stone your costs go up. The subcontracting for utilities and many other items will cost the same as for any house he continued, and if you decide to add a basement that adds lots of expense. If you just want storage, you can do it economically with a large attached garage which can accommodate recreational vehicles, shops, or even horses.
If you are not an experienced barndominium builder Gruhlke said, you need to ensure you have a viable, buildable plan and work with reputable subcontractors to get it done. His final piece of advice: “Know up front that in every project, something comes up to add on to the expense and/or the timeline.”