Early Post Frame
Post-frame construction first came into use in the 1930s when midwestern farmers found a quicker, easier and cheaper way to build barns and sheds. Old utility poles were often used, and people began calling these buildings pole barns. Every once in a while, one of these old buildings comes to light as people work to restore them. Often they are in need of drastic repair because when they needed upkeep, people often abandoned them for new buildings that require less maintenance and post-frame buildings were left to rot.
It is pretty amazing that after years of neglect, some of these structures survive today. “Pole buildings”, often called post-frame buildings today, are generally built with much improved components, processes, and craftsmanship. Imagine how long one of these newer buildings, if properly maintained, could last.
How Do You Build Longer Lasting Structures?
Barndos are, of course, not “pole barns”; the building processes and components of a barndo have come a long way from those old barns. Naturally the best way to ensure a building’s durability is to start with quality components, and apply old-fashioned pride and craftsmanship along with the best processes currently available.
Whether you are a DIY builder or you have hired a contractor to provide a turnkey home, you will want to understand some of the basic improvements that can help to ensure that your home will last for generations. While we will be unable to cover every possible item that could help with longevity, we will cover some important considerations related to the integrity of your home.
Trusses
Among the first improvements to post-frame buildings were pre-fabricated trusses. These trusses are pre-engineered, so they are ready to go without the roofer having to do math onsite to figure out how to build the trusses when they are trying to get the roof on. Further, heavy duty truss plates were invented which reinforce the trusses, increasing their stability.
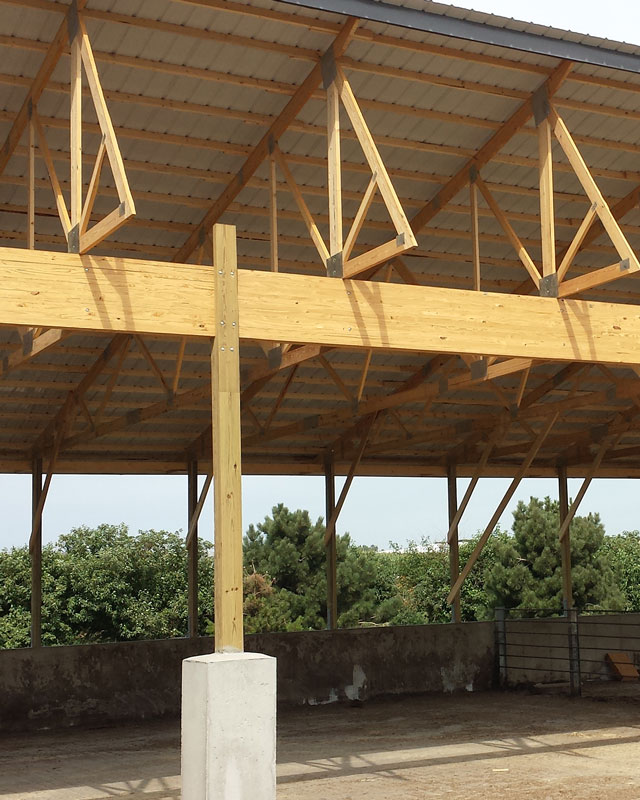
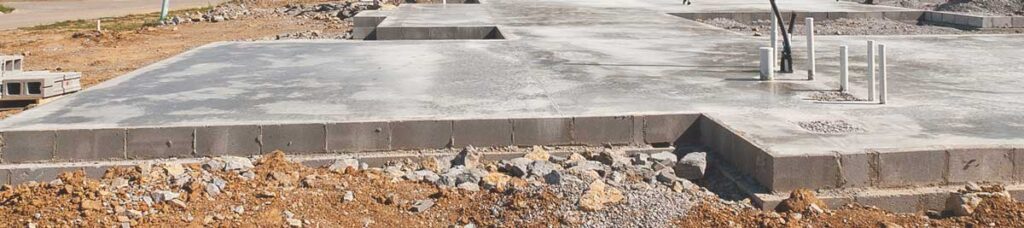
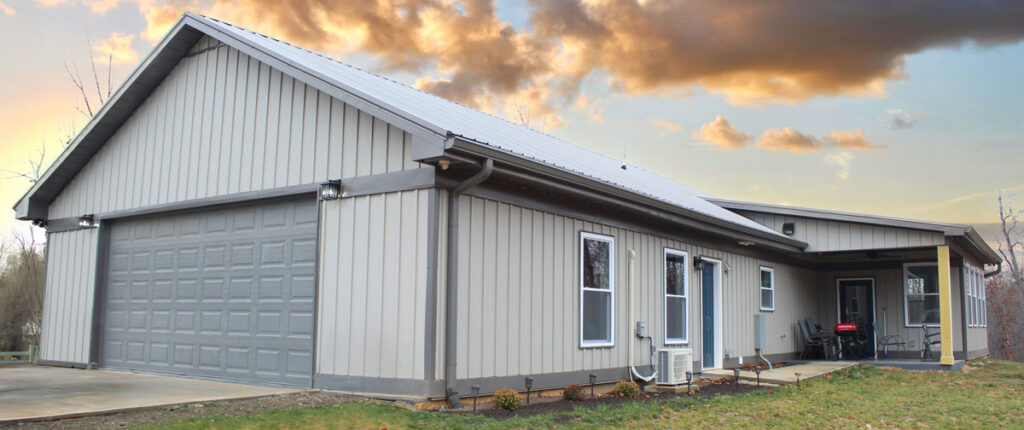
Site and Foundation
If your building is to last many years, site preparation and the foundation are very important. For example, if the site is level in a wet climate, the ground right by the building should be sloped away from the building so water doesn’t pool there. Drainage tile can be installed to help with drainage.
Post-frame foundations are often concrete slabs, either floating or monolithic. The monolithic slab is generally more solid and long-lasting because the concrete is continuously poured to include the concrete floor and concrete footers, which extend below the frost line to transfer the weight of the home to more stable ground. The posts and walls are installed atop the footings. Monolithic slabs are great in rocky areas, but they are risky in areas that are susceptible to the frost-thaw cycle. When you make a floating slab, the footers and walls are not actually attached to the slab/floor. Overall slabs can last up to 50 or 100 years or more, but they may have problems in areas where flooding is an issue because they are so low to the ground. All footings should be packed with a granular backfill so that moisture will drain away.
Stem walls are another option that is often adopted in areas with uneven ground, especially where soil erosion or shifting ground is an issue, and the slab will be elevated which helps in a flood situation. Footings are sunk in the ground, and blocks, usually concrete, are placed and built up to form the stem wall. Then the slab is poured over the stem wall and the posts are anchored to the slab. A builder can opt to pour the stem wall using wood as a form, then the anchor can be embedded in the stem wall. Sometimes the stem wall is reinforced with rebar for stability. Some builders opt to leave the slab unattached to the stem wall; it floats inside the walls which can help with soil heave. Like the previous slab options, this foundation can last from 50 years to well over one hundred.
A pier and beam foundation elevates the building so that a crawl space is created that has benefits like greater access to plumbing and electrical lines, but more to the point for our discussion, it creates greater stability on a sloped site, and due to the building’s elevation, there is less likelihood of flooding. The pier and beam foundation is more resistant to seismic activity, so if it is common in the area, this is a choice to consider. However, in general, pier and beam foundations may last only 15 years, unless maintenance is kept up, such as moisture mitigation and repair if needed, checking for pests, and pest removal. If carefully maintained, this type of foundation can last up to 50 years.
In summary, when you are looking for a long-lasting foundation, several things must be taken into consideration: climate, the location of the groundwater table for moisture considerations, the bearing capacity of the soil, and previous uses of the site – are there chemicals or other lingering effects which the structure will have to contend with?
DIYers should check with the area building codes and consider consulting an engineer or other knowledgeable local building professional.
Posts
The load bearing posts are, of course, an important piece of post-frame construction. Initially they were timbers, squared or rounded to fit into holes in the ground, then braced with horizontal beams.
Over time, builders and building owners began to see rotting of the post sections that were placed directly in the ground. Chemicals were found that would help to protect the posts, and builders began using posts that were treated to avoid rotting and pest abuse. The treatments used helped to keep the posts in good shape much longer, sometimes they can even outlive the pole buildings they framed. Still, wood placed directly in the ground is not the best way to ensure that even twenty years down the road, the wood is still protected.
Innovators in the post-frame construction industry began looking for solutions to this problem, and many have been developed. There are sleeves that can be placed over the posts to create barriers that keep moisture away from the section of the post in the ground. There are products that are baked until they bond with the wood, creating a surface that is virtually impermeable. There are also concrete columns that are sunk in the ground to create a pedestal for the post to connect to the pole above the surface. Which solution you choose can depend on things like pricing, climate, and the location of the water table. When you are building your home, it is a big investment of resources, and pressure treated wood along with one of these forms of added protection is the surest way to go.
Post Spacing
Another way to help ensure longevity is to place the posts close enough to ensure that the structure is not overstressed. This can be established in a couple different ways. If the building has engineering plans, the spacing will have been specified. If the building has no engineering plans, the builder will need to consult established framing tables. The guidelines should be available at the American Wood Council or the NFBA.
Fasteners
The fasteners used are important; they’re holding everything together. The materials used must be compatible with the type of fastener used. If the fastener will be exposed to the weather, fasteners with corrosion-resistant coatings should be used. If the building is in an area that experiences seismic activity, locking fasteners or thread locking compound should be applied.
Roofing and Siding
Metal is the go-to roofing and siding for post-frame. However, all metal is not the same. Metal gauge, or thickness, should be considered. The thicker the panel is, the lower the gauge becomes. 29-gauge is the standard for many projects; 26 gauge is thicker. It is advised that 26 gauge is used for a home. If your home is being built where there is a lot of snowfall, it is advisable to go with 24 gauge metal to handle the snowload.
That said, gauge is not all that matters. When purchasing or discussing metal roof and siding panels, ask for the tensile strength of the metal. Tensile strength, or hardness, is a measure of the stress the panel can handle before it breaks, and it is expressed in pounds per square inch.
Metal Tensile Strength Examples
Grade 80 = 80,000 psi
Grade 50 = 65,000 psi
Grade 40 = 55,000 psi
The tensile strength grades can go lower and higher than shown, though 45,000 psi to 80,000 psi is common for residential roofs. A higher grade combined with a lower, thicker gauge will be more durable.
Insulation
Investing in quality insulation that makes sense in your climate can be an important factor in the life of your barndominium; it keeps the home more stable. You may want to choose insulation that will not end up settling and flattening out. Rigid board or spray foam are considered good choices as they can help prevent moisture problems and reflective insulation can help too, especially in warm climates.
In addition to the insulation, try to ensure that all spaces around doors and windows, anywhere that air could get through is caulked or weather stripped.
In Summation
Considerations for building a home that will last for generations:
• The quality of the components that go into building the house
• The climate you are building in
• The soil makeup on your site
• How deep is the groundwater table?
• The expertise and craftsmanship of the builder/s
Resources: AcuformEquipment.com, McElroyMetal.com, SherwinWilliams.com, DrexMet.com, WickBuildings.com, GreinerBuildings.com, FBiBuildings.com, ManseaMetal.com, e2engineers.com